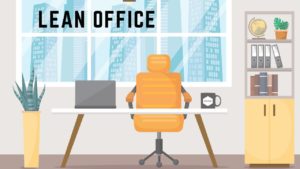
In simple terms, the lean office is defined as the application of lean management principles or lean philosophy to the front end processes. It was Toyota manufacturing that developed the concept of lean, in which they identified eight primary categories of waste that are produced in processes. They are inventory, transportation, waiting, motion, our production, Mnemonics, over-processing, and defects.
The concept of the lean office is relatively new to the market, and there are many views on how it should be achieved successfully. Some believe that eliminating waste is more complicated than increasing productivity because garbage is more quantifiable and then productivity.
Achieving lean office should be considered as an achievement for the company. There is never fully or entirely lean office. There is the less lean office, and then there is a more lean office but every office tries to move on the Lean vs Regular scale by moving towards leanness.
Principles of Lean Office
1. Committed leadership team
The lean office starts with a dedicated leadership team. These leaders can provide the foundation on top of which all the efforts of lean are built. They help to develop a strategy and create a revision to achieve the goals of the organization.
They understand the values of the content employee, and they empower the frontline team to create job satisfaction. There can be a lot of success with the company, but until the top management commits, lean will not be possible. It is the combined effort of frontline as well as senior management in sync with middle management.
2. Measurable metrics and goals are required for the lean office
It will be challenging to measure the output or the effect of change without metrics. The goals should be measurable so that the organization can work upon it and improve if necessary or change or delegate it to someone else. All of this can be done if the goals and objectives are measurable.
3. Standardize processes
People often follow different methods to do the same job. This would not work when the purpose of the organization is to achieve lean. Procedures should be standardized, and personal preferences should be set aside for official work. Also, if there are no standards set, then it would be inconvenient to improve the process. This will be applicable for the entire team so that consistency is achieved in their normal operations.
4. Lean office uses 5S
The absence of 5S is the indicator of a disorganized office. The chaotic office will be ineffective in terms of productivity. This is the reason why a standard needs to be established, and every employee should follow the office processes. It is essential to put things where they are most useful and reduce the clutter.
5S is a workplace organization method that is based on the principles of the sort, set an order, standardize, shine, and finally sustain. It is easy to confuse the law of 5S with lean, but both are different, and yet 5S is used in the principles of lean.
5. Minimum work in progress
One of the primary goals of the year is to reduce the work in progress process. It either tries to reduce or eliminate so that the time can speed up, and there is a rise in the consistency. This also means that the customer experience is improved, and it reduces a significant source of waste from the organization.
6. To achieve flow
The art of completing the process of the work from start to end with the help of the shortest means possible is called flow. It should happen without stopping or waiting in a queue.
The goal is to reduce the waiting time or eliminate it so that the time required to complete the process is minimum. Achieving flow in every process is very difficult, but once you reach it, it will work wonders for your office.
7. Understanding Demand
One of the primary challenges in making the office lean is to understand the vast variations that are often present in the process of demand. Demand is relatively easy to manage on the shop floor. But on the other hand, in the office, it is challenging to handle.
For example, a customer will not wait on the call for a long time, and you cannot answer every phone call before it rings. It is challenging to hold items in inventory if you are unable to manage the demand.
It is impossible to get approved of every loan application before the applicant needs money. One of the crucial factors which are equally complicated is that all the office work should not be considered as a demand. For example, processing orders and checking the status of the order is the work that has to be done, but it cannot be considered productive.
This does not mean that you should abandon these processes. Understanding these related tasks which make the big task possible is very important to make the office lean.
8. Daily Management System
Lean offices often use a daily management system. It is because they use a conventional management system that they are successful. Once you figure out the demand, then you need to have a management system that will manage the market.
The daily management system does just that. It is expected that the management system matches the demand for staffing and, more importantly, monitoring and proactive response are required in it. The control is necessary if the team falls behind the pre-decided plan.
9. Visual
It is effortless to manage teamwork, communication, and other things if the office is open for everyone. If anyone can walk and see what is going on in your work area, it becomes straightforward to comprehend the functioning.
The office is mostly in the form of ones and zeros like a computer language, and it is challenging to understand what is happening all at once. Visualization is essential to understand this. Visualizing in office will help to normalize situations.
10. Clear communication and teamwork
A lean office has clear communication between co-workers. Having clear communication is one of the essential criteria for successful collaboration. There could be many times when the miscommunication is happening, which would potentially impact the business. It is, therefore, necessary to clarify everything before committing anything.
Co-workers, bosses, senior management people should always be communicated in a clear and precise language. It works both ways as the downward communication should also follow clearly. Good teamwork is one of the defining characteristics of a lean office. People should be responsive to changes in demand and should be flexible about it.
11. Continuous improvement
As the lean office is a continuous process to maintain it, it requires a long commitment over time. There must be constant development and growth in the process as the time demands.
It takes many years to accomplish this, to make everyone understand and regulate the process of waste reduction.
Designing a Lean office
As mentioned earlier, it was Toyota that identified key areas where the waste can be reduced. When it identified them, they were only targeted for manufacturing processes. But now it can be extended even to an office environment and can be applied there.
Overproduction could mean a lot of paperwork and multiple approvals. To decrease these times, there are many areas of wastage which should be pointed out and worked upon to eliminate them. Value stream mapping is one of the processes used for streamlining manufacturing. This allows even offices to have a map of the entire process right from the time when the customer places the order until the order is delivered to him.
When the mapping is carried out, ideally, it should be summarised and understood by at least one person or a team together. This is useful because it will help them to understand the entire process thoroughly instead of someone explaining to them, and every person in the organization understands it bit by bit and makes his assumptions.
Only when this is completed, then the work on a future map can be initiated with the help of lean principles. The primary objective is always to eliminate waste, unnecessary paperwork, and several multiple approvals to increase efficiency and reduce time.
The post What is a Lean Office? Principles and Design of a Lean Office appeared first on Marketing91